Have you wondered what is inside the Phantom 4 body? Ever since the Phantom 4 landed in our office, the engineers have wanted to take a look inside the quadcopter, curious to find out 'what's improved this time?'. By now we had all seen the most-advanced-technology video on the DJI Youtube channel. Released as part of the product launch it gave a top level insight into what goes on inside the new Phantom. We wanted to go past the 3D 'exploded animation' and discover just how difficult it would be to service or repair the drone. Please note : This is not intended to be an instructive guide (such as those found on ifixit) for dismantling your drone, but more a documentation of our investigation into the architecture of the new quadcopter. We take no responsibility for any potentially warranty-invalidating work carried out on your Phantom by yourself, it is at your own risk.
As per previous models, the camera and gimbal are one unit and we'd recommend beginning here (once you have removed the battery). The gimbal is held on by 8x 1.5mm hex screws on the light grey composite belly of the craft (labelled in blue above). When these have been removed, run a plastic tool around the edge of the gimbal plate to release the clips that retain it. You can see the locations in the photo below.
Carefully lower the camera and gimbal and undo the two ribbon cables (one of a lever type) that connect it to the flight controller board. This can now be moved out of the way. With the gimbal removed you can access the cross head screws on white tabs holding the composite internal frame to the lower shell. Next there are 8 hex screws, one at the arm/body transition and one half way down each arm. They are marked in red on the initial diagram.
The plastic light diffuser (as seen in the above photo) on the arm under each motor simply pop off with a flat head screwdriver. There is a small piece of white card taped down as a reflector for the LED, remove this and reveal a further 3x 2mm hex bolts per arm. With all of these removed, run a plastic tool around the seam in the upper shell, releasing each of the clips as you go. Take your time as to not damage these.
Unplug the two grey compass cables and remove all four of the push-on antenna connections for the lightbridge.
Finally the entire top half of the craft lifts off taking the internal chassis and electronics with it, leaving the compass and antenna in the legs below. The teardown continues from here, disconnecting the cables and ribbons from the power and speed controller boards to the main section, unscrewing them from the core before unscrewing the core itself from the top shell to carefully remove it.
The main processing board sits on the bottom of the composite core, cooled by a large heatsink and the fan in the gimbal. The flight controller is stacked with the logging SD card visible.
The leading edge of the core has mounts for the front visual sensors, connected to the board via ribbon cables.
The composite core also features the lower VPS visual and ultrasonic sensors for vertical distance calculations.
On the underside you can see the full length foam rubber landing pads with markers to aid installation of the gimbal.
Motors are located on a set of posts, locating them before the body screws hold them in place.
Motor and LED cables run the length of the arms beneath the upper case.
The lower shell slots onto the upper shell shown in the previous photo
A ribbon cable from the flight controller feeds the control information to each board, you can see the connector on the top leading edge.
The daughter boards are fed via plugs on its edge and a ribbon control cable pictured on the right in the image below.
The battery connector has (thankfully) been totally redesigned from all of the previous phantoms. It is now a 10 pin plug with metal surround protecting it. Externally it makes charging the battery easier as its reversible. Internally there is much less chance of the battery becoming disconnected during flight compared to the sprung pins.
The top of the body is lined with soft padding and copper insulation film protecting the GLONAS/GPS module that lives in the lid.
Battery installed without composite internal frame to demonstrate location.
The battery has a set of guides molded into its casing that line up with markers on the composite core.
Battery removed from the upper body and placed aside for scale.
Internally a small fan blows air through the perforated bottom plate over the heat sink on the core. The board itself is connected to the rest of the electronics via two ribbon cables.
On the outside the new gimbal mount is beautifully designed out of matt finished plastic.
The gimbal itself has been upgraded with dual motors for the tilt axis, this secondary mounting point will potentially reduce shake.
The frame components laid out in order.
Overall we feel that it is slightly more involved than deconstructing the Phantom 2/3, due to the well-packaged design.
Further information about the Phantom 4, or to place an order, check-out the Phantom 4 Quadcopter on our website. If you have crashed or damaged your drone, please get in contact with us here and we will endeavor to help. Full details of our Phantom and Inspire 1 repair service will be released later this month. If you have any questions regarding this basic teardown, or require any further images please leave a comment below.
Tools required

- 2mm Hex Driver
- 1.5mm Hex Driver
- Small Cross-head
- Small flathead
- Plastic spudger
- Trim removal tool
Teardown : Dismantling the Phantom 4
The major difference this teardown revealed is that unlike previous Phantom's, the Phantom 4 has all its hardware connected to the 'lid' of the shell; Bear this in mind when removing it. To start we've put together this diagram showing the location and size of the bolts on the outside of the craft.
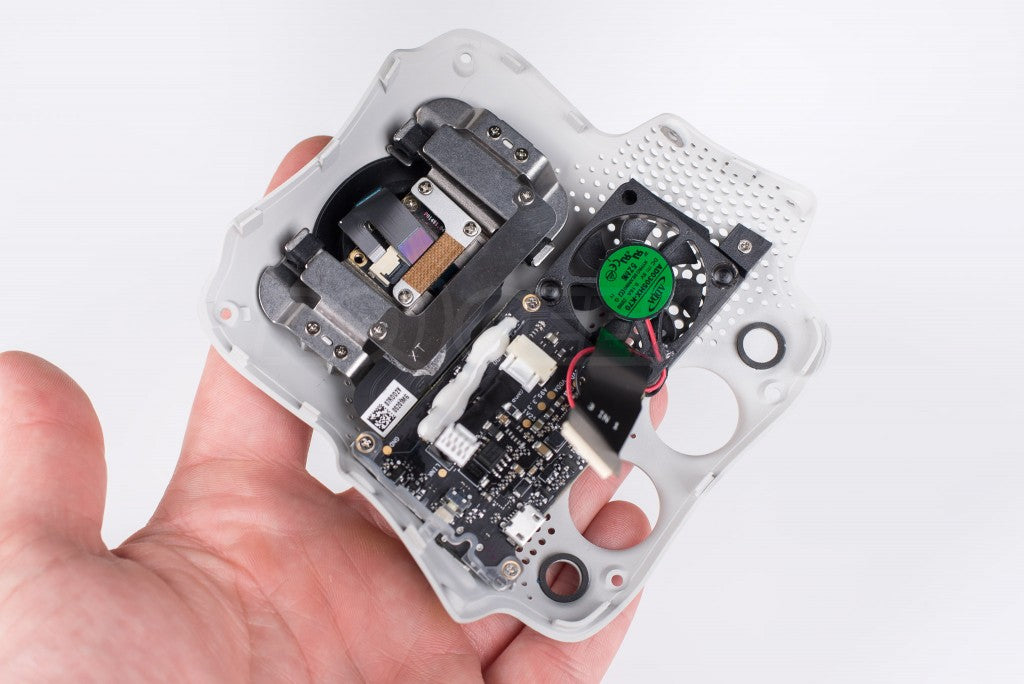






Lower shell, Landing gear and Antenna
The lower shell is made of lightweight plastic and houses the antennas and compass in the legs, running the wires internally.
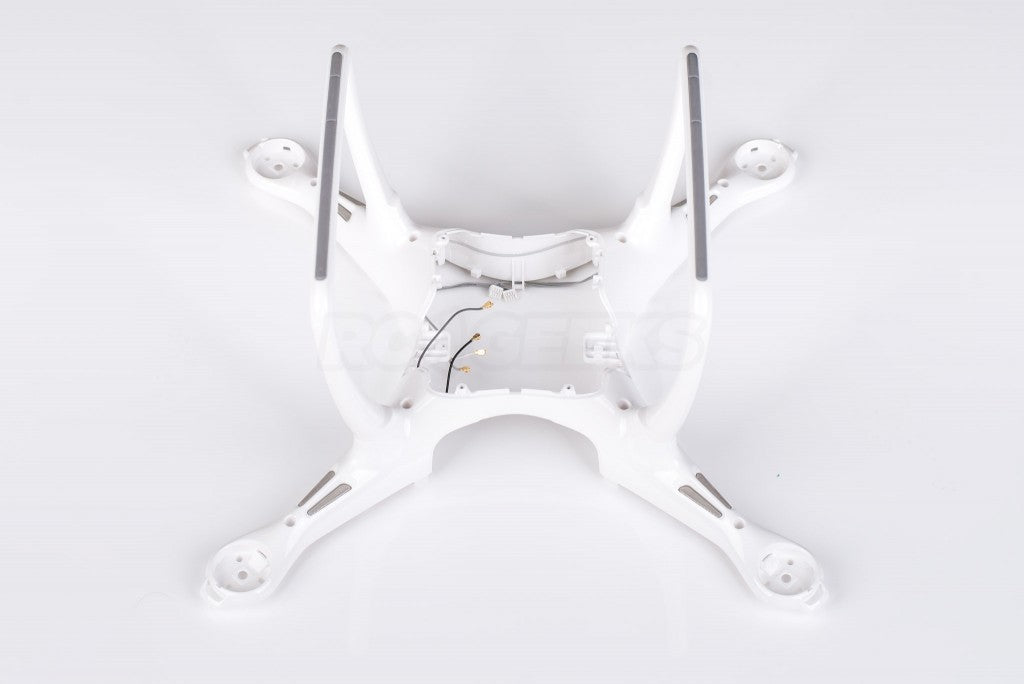
Motors and Mounting




New ESC (Electronic Speed controllers)
The phantom 4 features all new speed controllers. The boards are mounted vertically, screwing into the sides of the magnesium core. Each ESC controls a pair of motors (one CW and one CCW) a pair of LED's and has a power feed to the main distribution board.

Power distribution and Battery connector
The power distribution board now sits at the front of the drone with twin outputs.





New Gimbal/Camera mount and electronics
The passive dampening of the gimbal has been moved into the craft, allowing for a cleaner more aerodynamic profile externally. The new gimbal damper employs a series of bushing materials to cushion its motion and appears a lot hardier than the previous rubber dampers.


Teardown component overview


